Desiccant Rotors ProFlute PPS Silicagel 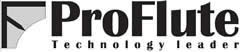
Why does ProFlute call itself “Technology Leader”?
You only have to compare the dehumidification performance of ProFlute rotors to other types on the market!
Why does ProFlute call itself “Technology Leader”?
You only have to compare the dehumidification performance of ProFlute rotors to other types on the market!
Rotor designs
Depending on the requirement, ProFlute rotors offer:
When comparing the dehumidification system operating costs it is important to check the required power for both the process and reactivation air fan. These fans are operated 24 hours per day, 7 days per week at full power.
Based on your requirements such as dry air data , pressure loss, reactivation energy available, etc. we can recommend you the optimal rotor and operating data. Send us your system requirements – we will document the lead of ProFlute PPS in rotor technology.
Rotor Material Composition
The ProFlute PPS rotor has a very high, 82%, active SilicaGel content and only 16% glass fibre content, the remaining 2 % is the Acrylic surface coating
Fire Resistance
The PPS rotor has been tested according to ASTME test E-84 and achieved a flame index of 0 and a smoke produced of 0. This means that the rotor is inflammable and will not produce smoke.
Technical Properties
There is no limit for how high relative humidity the rotor can stand as long as droplets are not introduced into the rotor during operation. The PPS rotor can be washed in water with weak non-alkaline detergent, after saturation in humid air.
Physical Properties
The density of dry material is approx. 240 kg/m3. The PPS media can pick up approx. 40% of it’s dry weight as moisture in humid environment.
The surface compression strength of the rotor is more than 200 kPa.